Leak Repair of Paper Mill Drier Cylinder
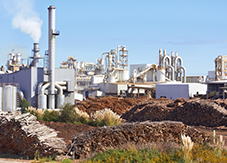
Damaged valves prevented standard isolation and replacement of large leaking bellows. TEAM designed, manufactured and installed a close-fitting bespoke encapsulation box as a solution.
SCA Hygiene’s on-site maintenance TEAM noticed that wet steam was leaking out of the ‘Yankee drier’ cylinder at the end joints, with the result that the paper was not drying effectively, pressure had to be reduced, and production was therefore compromised. Traditionally the solution would be replacement, but this would have involved a costly, unplanned shutdown, potentially of as much as two weeks, as well as waiting for delivery, plus challenging logistics and lifting equipment requirements.
TEAM applied its tried and tested leak-sealing technology to the new application, producing a bespoke solution. This involved removal of all the existing fasteners and bolts on both ends of the drier, installation of special ring adaptors under the new bolts, and injection of the peripheral jointareas with a special-sealing compound. The compound was designed to the tolerances of the drier, ensuring that it would not react to the change in operating temperature from 8 bar steam to ambient when shutdown.
The work, undertaken during a scheduled outage with engineers under tight time limits to complete the job, included changing out and injecting as many as 600 bolts on the 12-foot cylinder. It was completed, working night and day shifts, in just a 4-day period.
The solution has been so successful that TEAM technicians are worked with SCA Hygiene TEAMs in Italy on the wider implementation of the solution.